A Comprehensive Guide to Welding Assessment Techniques and Best Practices for Quality Control in Fabrication Projects
Welding examination serves as a fundamental pillar in making certain the architectural integrity and safety of made projects. Using a variety of methods-- ranging from aesthetic analyses to advanced methods like radiographic and ultrasonic testing-- supplies crucial insights into prospective flaws that might weaken toughness. Establishing effective practices and a robust quality management system can enhance compliance and reliability. Nevertheless, the complexities of these methods and their application typically increase pertinent questions about the standards and tools essential for optimum end results. What particular methodologies will be most effective in your tasks?
Significance of Welding Inspection
Welding examination is an essential part in making certain the stability and safety and security of welded frameworks. The process includes a systematic examination of welds to determine any problems that might endanger the strength and sturdiness of the last product. Reliable evaluation is crucial not only for conformity with sector standards and guidelines but likewise for guarding the health and wellness of employees and the public.

In addition, welding inspection offers as a beneficial device for continuous enhancement in manufacture procedures. Ultimately, focusing on welding evaluation fosters a culture of quality guarantee, making certain that tasks fulfill both client expectations and regulatory requirements.
Common Welding Inspection Strategies
Various methods are employed to check welds, each tailored to detect certain types of problems and make certain high quality. Amongst one of the most generally made use of methods are aesthetic examination, ultrasonic testing, radiographic screening, magnetic particle testing, and dye penetrant screening.
Visual inspection is the most straightforward technique, permitting examiners to recognize surface area abnormalities such as cracks, porosity, and damaging. Ultrasonic testing uses high-frequency acoustic waves to discover interior problems, providing an extensive evaluation of weld stability. Radiographic screening makes use of X-rays or gamma rays to develop photos of the weld, disclosing internal defects that are not visible to the naked eye.
Magnetic particle testing is particularly effective for ferromagnetic materials, identifying surface and near-surface defects by applying magnetic fields and utilizing fine fragments that show abnormalities. Color penetrant screening includes using a tinted dye to the weld surface, which seeps right into splits and is disclosed under ultraviolet light, making it very easy to detect issues.
Each of these methods plays a critical duty in maintaining welding quality, and the option of an ideal approach depends upon the details needs of the manufacture job, including product kind, weld configuration, and the wanted degree of evaluation.
Vital Inspection Tools
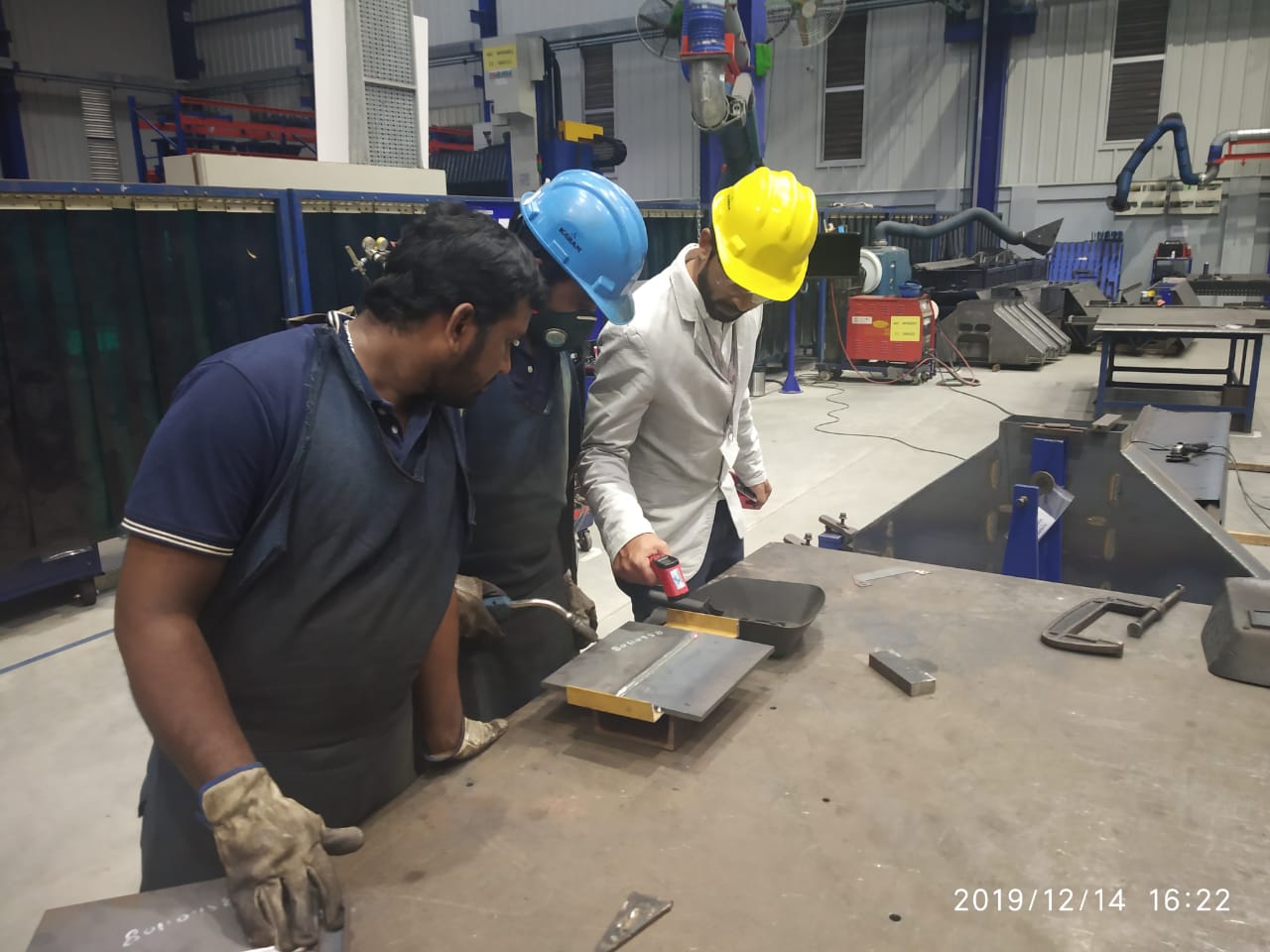
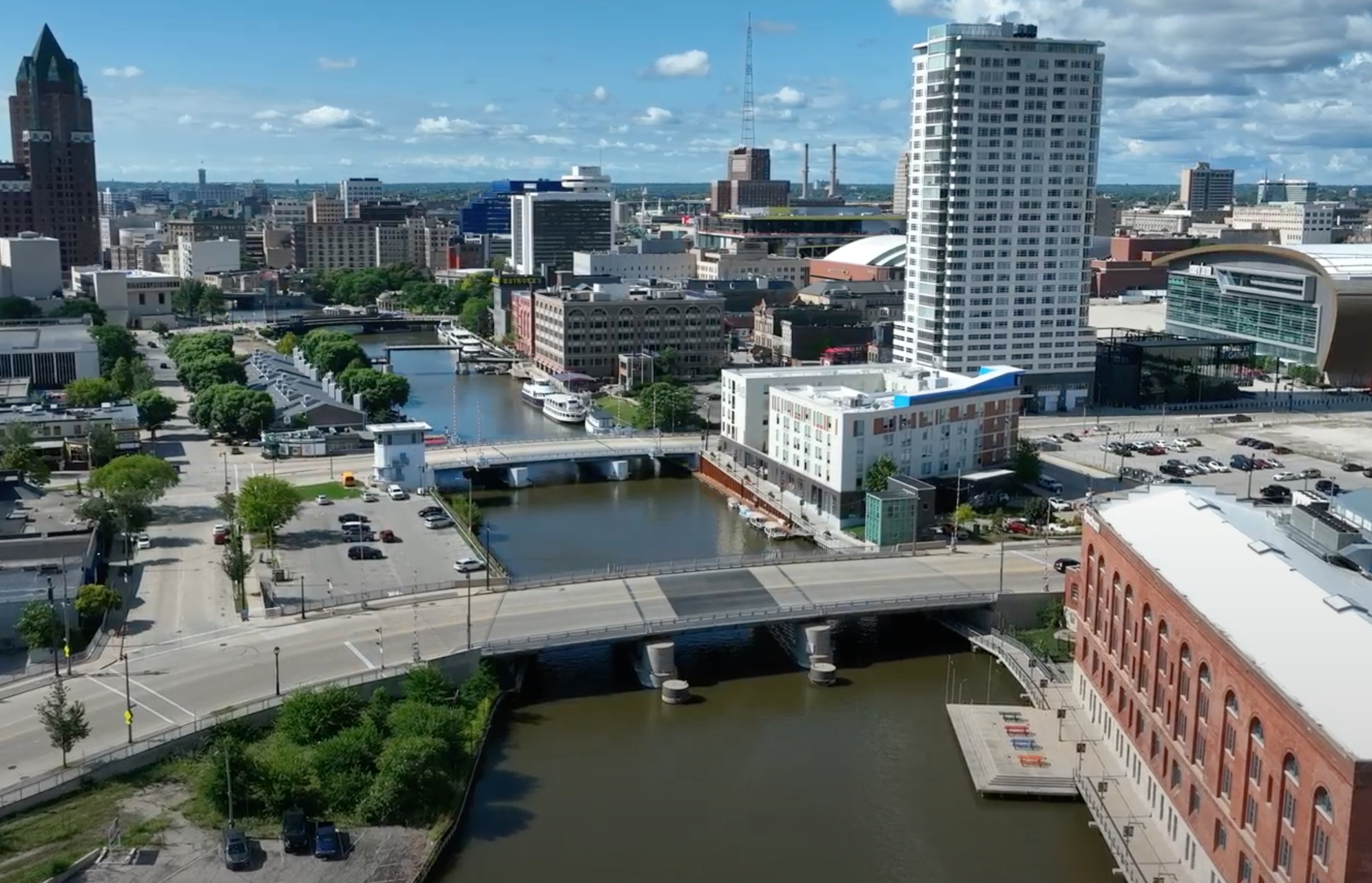
Gauging devices, consisting of calipers, gauges, and leaders, are vital for validating tolerances and measurements. These tools help make sure that welds meet the needed specs for stamina and sturdiness. In addition, ultrasonic screening gadgets are utilized to find inner imperfections without compromising the stability of the weld. This non-destructive testing approach see here is important for recognizing concerns that may not show up externally.
An additional indispensable tool is the solidity tester, which evaluates the mechanical homes of a weld and establishes its viability for details applications. Ultimately, welding assessment software help in recording findings, promoting data evaluation, and making certain compliance with market requirements. Together, these crucial inspection tools form an extensive toolbox that sustains the welding assessment procedure, inevitably adding to the top quality assurance of fabrication projects.
Best Practices for Quality Control
In the pursuit of quality control, implementing best techniques is crucial for attaining regular and trusted welding end results. Developing a detailed welding high quality management system (WQMS) is fundamental. This system ought to include defined procedures, criteria, and paperwork methods that direct every stage of the welding procedure.
Routine training and qualification of welding personnel are crucial. Experienced welders with updated expertise of methods and safety actions add substantially to quality. Carrying out pre-welding inspections ensures that products and equipment fulfill specified requirements, reducing the probability of defects.
Including real-time monitoring throughout the welding process permits immediate discovery of abnormalities, allowing rehabilitative actions to be taken immediately. Post-welding inspections, including aesthetic checks and non-destructive screening (NDT), are important in verifying weld stability and conformity with industry requirements.
In addition, maintaining precise documents of inspections, weld parameters, and restorative actions promotes a society of accountability and continuous renovation. Engaging stakeholders in normal quality testimonials can also boost the overall efficiency of quality assurance procedures. By sticking to these ideal techniques, organizations can substantially boost their welding top quality guarantee initiatives, therefore ensuring project success and client complete satisfaction.
Enhancing Security and Compliance
Achieving high standards in welding high quality assurance naturally lines up with the critical of boosting safety and security and conformity within the market. Efficient welding inspection techniques are vital in ensuring and recognizing possible dangers that all processes stick to regulative requirements. These methods not only offer to maintain architectural integrity but additionally secure the health and wellness of personnel associated with construction projects.
Applying extensive evaluation methods, such as visual examinations, non-destructive screening (NDT), and detailed documents, establishes a society of safety and liability. Training welders and examiners in current security regulations and finest practices is necessary. This guarantees that all employee recognize potential dangers and are equipped to alleviate them.
Moreover, compliance with market standards, such as those established by the American Welding Society (AWS) and the International Company for Standardization (ISO), is non-negotiable. Normal you could look here audits and assessments assist recognize gaps in security actions and promote constant enhancement - Welding Inspection Milwaukee. Eventually, a dedication to boosting safety and compliance not only cultivates a more secure working environment however additionally leads to exceptional high quality end results and reduced liability for organizations taken part in welding here are the findings construction
Verdict
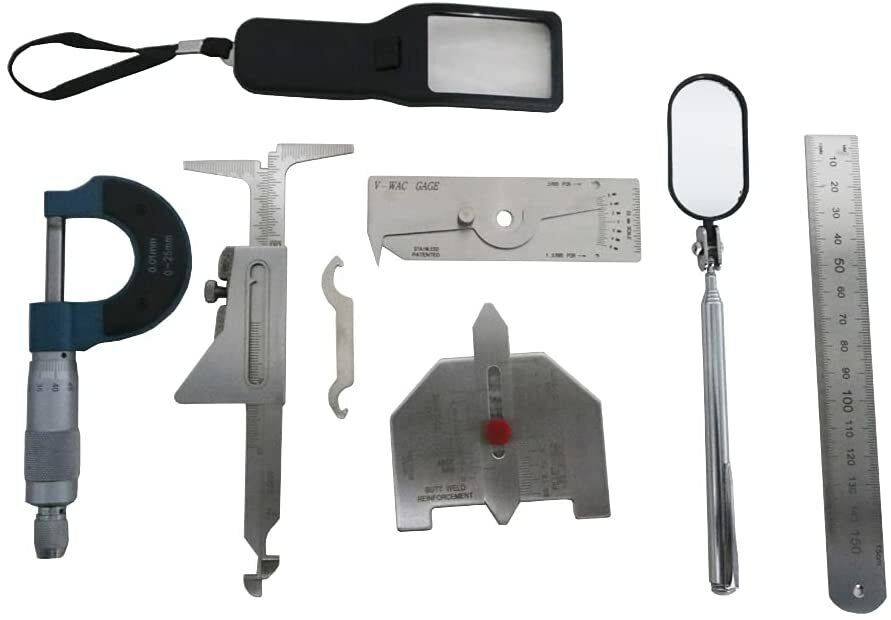
Welding evaluation serves as a fundamental column in making sure the architectural integrity and safety of fabricated projects.Welding evaluation is an important part in making sure the honesty and security of bonded frameworks. Eventually, prioritizing welding evaluation promotes a culture of quality guarantee, making certain that tasks satisfy both client expectations and regulatory needs. Together, these essential inspection devices develop an extensive arsenal that sustains the welding assessment process, ultimately adding to the high quality assurance of manufacture jobs.
In verdict, reliable welding assessment is crucial for making sure the structural honesty and security of made jobs. Welding Inspection Milwaukee.